技术支持
地 址:湖南省安化县高明乡工业园
手 机:137-8611-1081
电 话:0737-7411519
传 真:0737-7411519
联系人:薛经理
Q Q:28288453

碳化钨生产工艺
时间:2015-10-25 17:38:49来源:本站人气:3018
一、炉料计算
炉料中炭黑配量按下式计算:

式中Qc—炭黑配量,公斤;
C—碳化钨中要求的含碳量,%;
O2—钨粉中含氧量,%;
Qw—钨粉的重量,公斤;
0.75—系数,碳与氧原子量之比值。
如果配炭不准,所得碳化钨的含碳量不合格,则必须补加钨粉或炭黑,并重新碳化。
碳化钨中含碳量低时,其炭黑补加量按下式计算:

式中Cx—炭黑补加量,公斤;
CA—碳化钨中要求的含碳量,%;
CB—碳化钨实际含碳量,%;
Q—碳化钨的重量,公斤。
例如,一批重205公斤的碳化钨经分析总碳偏低,仅为5.5%,而所要求的含碳量为6.0%,则炭黑补加量应为:

碳化钨中含碳量高时,其钨粉补加量按下式计算:

CA和CB—见公式(3—9)的式中。
例如,一批重210公斤的碳化钨,经分析含碳量为6.20%,而所要求的含碳量为5.90%,则钨粉补加量应为:

配炭计算时可按碳化钨粉技术条件,取其中间值。考虑到碳化过程中石墨管和舟皿将向炉料中渗入少量碳,因此炭黑配量未按炭黑所含的固定碳计算。为了减少因计算带来的差错,生产中通常按配炭表(见表3—3)进行配料,并根据钨粉含氧量适当增加炭黑量,见表3-4;同时还应根据气候的变化和地区的不同加以适当调整。在空气湿度大的季节和地区,因炭黑含水量较高,配炭时适当增加炭黑配量;反之,在空气湿度小的季节和地区,可适当减少炭黑配量。炭黑的称量应力求准确。
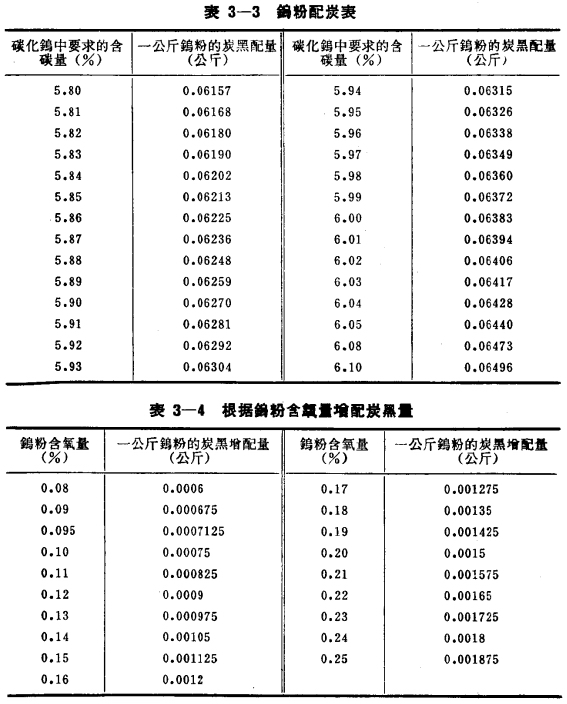
钨粉与炭黑混合均匀与否很重要,如果混合不匀,碳化时将出现黑心、分层等弊病。
钨粉与炭黑在球磨机内(球:料=1:1,钢球直径φ35~50毫米)混合2~4小时,用肉眼观察无分层现象即算均匀。在装料时,应先装钨粉后装炭黑,以免炭黑飞扬损失。
为了保证混合质量的稳定,混合时间,球料比不宜经常变动。粒度不同和含碳量范围不同的物料,最好固定专机混合。如果条件不允许,则在使用前球磨机内的物料必须清除干净,否则易于造成粒度不匀,炭量不准。混合后卸料应力求迅速,以缩短钢球在物料减少过程中互相撞击的时间,减少杂质铁的混入。
三、碳化
钨粉碳化在石墨管电炉中进行。其工艺条件见表3-5。
由于各种原因需要补加炭黑或钨粉重新碳化者,其重新碳化工艺条件见表3-6。
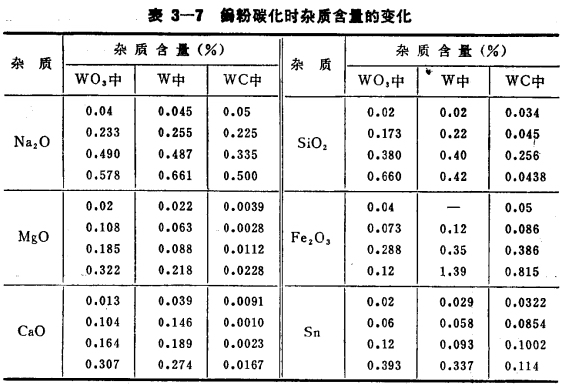
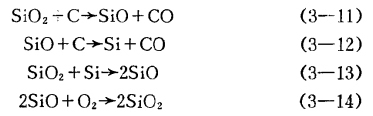
所生成的这些氧化物,也可能沉积在已碳化好的料块的表面上,因此在卸料时应仔细地将其刷去,以免影响碳化钨的质量。舟皿加盖可减少杂质落入。
如果石墨舟皿材质不好,容易被氧化而呈疏松多孔状,料块则容易粘附细小的石墨颗粒,经球磨过筛后,仍有少部分落入碳化钨粉中,在显微镜下观察时呈黑色发亮的小片。在物料与舟皿之间垫上无灰纸或者采用优质石墨作舟皿,可避免这种情况产生。
四、球磨、过筛和合批
球磨:碳化后的物料呈块状,须进行磨碎。磨碎在球磨机中进行,筒内装入直径10~45毫米的钢球200公斤,球与料之比为1:1,球磨时间根据具体情况而定,一般为2小时。
在球磨不同粒度的碳化钨时,应将球磨机清理干净,以免造成少量混料,使碳化钨粒度不均匀。为了减少碳化钨中混入杂质铁,球磨后卸料时间应尽量短。
球磨后碳化钨松装密度增大,这是由于在球磨过程中碳化钨颗粒之间收遨播擞丝蓝被破坯,使其表面平滑的缘故,而实际颗粒大小并没有显著变化。
过筛:过筛的目的是除去可能落入的夹杂物并使粉末松散。细颗粒过200目筛,中颗粒过250目筛,粗颗粒过60目筛。
为了防止粉末飞扬,过筛应在密闭情况下进行。球磨(或合批)后的料立即过筛,否则会因存放时间过长,使物料受潮(尤其细颗粒),难以过筛。
合批:是将两个单批的碳化钨粉放在螺旋混合器内混合2小时。
根据单批的物理化学分析检验结果,选择其碳量和松装密度都比较接近的单批进行合批。一般说来,在两个单批的含碳量和松装密度之差分别不超过0.1%和1.0克/厘米³的情况下,都可以合批。如果相差过大,会造成成分和粒度不均匀。
碳化钨合批后其松装密度约降低0.2克/厘米³,这是由于碳化钨经螺旋混合器混合后更加松散的缘故。
对于以橡胶作成型剂的合金生产工艺而言,合批(或单批)的碳化钨过筛后应取样分析和检验,其成分和松装密度应符合表3-8所列范围。
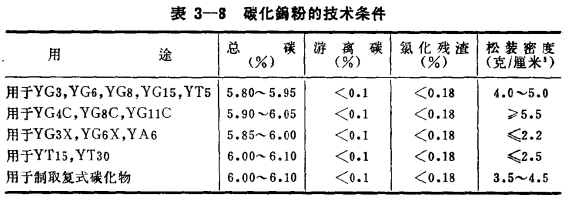
- 上一篇:金属钨粉制取的主要方法
- 下一篇:碳化钨硬质合金堆焊焊条