技术支持
地 址:湖南省安化县高明乡工业园
手 机:137-8611-1081
电 话:0737-7411519
传 真:0737-7411519
联系人:薛经理
Q Q:28288453

硬质合金可转位浅孔钻头的结构特点
时间:2015-08-04 15:59:29来源:本站人气:2290
(1)概述
硬质合金可转位浅孔钻是继60年代喷射钻取得成功之后的又一新的突破,且在机械加工中发挥了重要作用。当今世界上许多工业发达国家都能生产这种钻头。
硬质合金可转位浅孔钻的标准规格为直径20~60mm。但某些公司生产的这种钻头,其最小直径可达16mm左右,直径再小则受到刀片尺寸和夹紧元件的限制;专用的可转位钻头最大直径可达350mm,直径再大则受到机床传动功率的限制。
(2)硬质合金可转位浅孔钻的结构特点
①可转位浅孔钻的容屑槽有直槽和螺旋槽两种,其中直槽的占多数。因为直槽浅孔钻的冷却孔易于制造,且所占位置较小。
②切削部分刀片的配置形式如图9-135所示,常用的刀片有凸三边形、四边形、菱形。刀片的位置根据分屑原理和力的平衡原理设计,即一片刀片位于钻头中心,另一刀片位于钻头外缘,切削时两刀片把金属分成两部分。为了平衡两切削刃产生的切削力,一方面对位于钻心和外缘的两刀片的切削负荷进行合理地分配,另一方面把两切削刃分别配置在通过钻头轴线但与钻头轴线不对称的两个平面上,使两平面的夹角为β,其大小根据力的平衡原理推算。钻头两切削刃上的切削力(见图9-136)可按下式计算:
主切削力Fz=0.1ks·t·s(N)
轴向力 Fz=0.05ks·t·S(N)
式中,Ks与被加工材料、切削速度、几何参数有关,它是切下单位面积金属所需要的力。根据上述方法设计的钻头,在理想的情况下两切削刃产生的径向力相互抵消,为此切削力由一个扭矩和一个轴向力构成。
③钻头的几何参数
(a)φ角;它与选用的刀片形状有关,直接影响切削力各分力的大小和方向。为了使切削平稳,φ角设计得较小。如装凸三边形刀片的钻头φ=10°。这时的钻头切入与切出长度也相应缩短。
(b)前角。内切削刃位于钻心,切削速度低,这对切削刃极为不利。为此内切削刃前角γ=0°~10°。为了增强外刃强度,刃口应高于通过钻头轴线的平面,因此外刃前角较内刃前角小些。
(c)后角:在钻削中切削刃的运动轨迹是螺旋面,工作状态后角小于静止状态后角,切削刃上各点的后角不相等,越靠近中心后角越小,为此选择后角口=7°~9°。
④断屑是使可转位浅孔钻头正常工作不可缺少的条件,否则将发生切屑缠绕和堵塞现象,引起崩刃和打刀。由于可转位浅孔钻头的切削速度较高,切屑薄,不易断屑,所以用断屑槽来改变切屑流出的速度和方向,以达到断屑的目的。工具研究所介绍的断屑槽形状和尺寸如图9-137所示。试验表明,断屑槽的尺寸公差必须限制在很窄的范围内,特别是断屑槽的深度对断屑效果影响很大。
⑤刀片的卡固方式:可转位浅孔钻采用带孔刀片,靠刀片本身的沉头孔用沉头螺钉压紧(见图9-138a),沉头锥角为40°。但这种卡紧方法对刀片孔有扩张作用,且扭紧很费时间。为此,又有采用图9-138b所示的夹固方式。在这种结构上,偏心螺钉2以其锥面3压紧在刀片1的孔壁上,并把刀片压紧于基面和后定位面上。这时,只要轻轻转动螺钉即可松开或夹紧刀片。更换刀片时也不必完全旋出螺钉。这种卡紧方法还保证了足够的容屑空间,使切屑能顺利地排出。
⑥模块化结构;把刀体分成几段制造,然后组装成钻头,一旦前段损坏,则可去掉该段,再重新组装。相同或不同直径的钻头可通过不同的连接柄而装在机床上使用。
⑦冷却方法:用可转位浅孔钻头钻孔必须强制浇注冷却液,它起着冷却润滑和排屑的双重作用。冷却液的流路如图9-139所示。它又分为下述两种流路:
(a)冷却液从钻头体中段或尾端的孔流入钻头体,从位于钻头端部两个呈“丫”字形分布的孔流出,碰到已加工表面返回浇到切削区域后,带着切屑沿排屑沟排出孔外。
(b)冷却液从钻头体中段或尾端的孔流入钻头体,从位于钻头切削刃前面的两个出水孔流出浇到切削区域后返回,在返回途中带着切屑沿排屑沟排出孔外。
直径小的钻头可采用两种流路相结合的方式,以加强排屑的作用。
(3)钻头各部分尺寸的确定
①钻心直径:硬质合金浅孔钻头的钻心直径do=(0.25~0.5)D,D为钻头直径。由于刀杆内部钻有内冷却孔,故钻心直径不能太小。设计时一般取do=0.35D。
②钻头直径公差:刀片位置的偏差可使孔径扩大或缩小。此外,还有进给量的影响,进给量越大,孔的直径扩张量也越大。但切削速度增加时,则孔的直径可稍有缩小。孔的圆度和圆柱度,主要取决于工件一刀具一机床系统的刚性,一般不超过0.02mm,可取与硬质合金麻花钻头公差相同的值。如在车床上钻孔,当孔径在50mm以下时,圆度误差在0.02~0.06mm范围内。
③两切削刃的搭接量:以分屑方式配置的两切削刃的衔接处应有一定的搭接量,其数值为2~5mm。这样可使一种规格的刀片能用于多种规格的钻头上,减少了刀片规格。
硬质合金可转位浅孔钻的出现,使孔加工的切削效率空前提高。所以,使其得到了广泛的应用。
硬质合金可转位浅孔钻是继60年代喷射钻取得成功之后的又一新的突破,且在机械加工中发挥了重要作用。当今世界上许多工业发达国家都能生产这种钻头。
硬质合金可转位浅孔钻的标准规格为直径20~60mm。但某些公司生产的这种钻头,其最小直径可达16mm左右,直径再小则受到刀片尺寸和夹紧元件的限制;专用的可转位钻头最大直径可达350mm,直径再大则受到机床传动功率的限制。
(2)硬质合金可转位浅孔钻的结构特点
①可转位浅孔钻的容屑槽有直槽和螺旋槽两种,其中直槽的占多数。因为直槽浅孔钻的冷却孔易于制造,且所占位置较小。
②切削部分刀片的配置形式如图9-135所示,常用的刀片有凸三边形、四边形、菱形。刀片的位置根据分屑原理和力的平衡原理设计,即一片刀片位于钻头中心,另一刀片位于钻头外缘,切削时两刀片把金属分成两部分。为了平衡两切削刃产生的切削力,一方面对位于钻心和外缘的两刀片的切削负荷进行合理地分配,另一方面把两切削刃分别配置在通过钻头轴线但与钻头轴线不对称的两个平面上,使两平面的夹角为β,其大小根据力的平衡原理推算。钻头两切削刃上的切削力(见图9-136)可按下式计算:
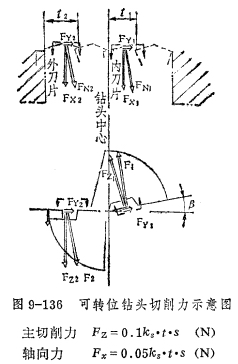
轴向力 Fz=0.05ks·t·S(N)
式中,Ks与被加工材料、切削速度、几何参数有关,它是切下单位面积金属所需要的力。根据上述方法设计的钻头,在理想的情况下两切削刃产生的径向力相互抵消,为此切削力由一个扭矩和一个轴向力构成。
③钻头的几何参数
(a)φ角;它与选用的刀片形状有关,直接影响切削力各分力的大小和方向。为了使切削平稳,φ角设计得较小。如装凸三边形刀片的钻头φ=10°。这时的钻头切入与切出长度也相应缩短。
(b)前角。内切削刃位于钻心,切削速度低,这对切削刃极为不利。为此内切削刃前角γ=0°~10°。为了增强外刃强度,刃口应高于通过钻头轴线的平面,因此外刃前角较内刃前角小些。
(c)后角:在钻削中切削刃的运动轨迹是螺旋面,工作状态后角小于静止状态后角,切削刃上各点的后角不相等,越靠近中心后角越小,为此选择后角口=7°~9°。
④断屑是使可转位浅孔钻头正常工作不可缺少的条件,否则将发生切屑缠绕和堵塞现象,引起崩刃和打刀。由于可转位浅孔钻头的切削速度较高,切屑薄,不易断屑,所以用断屑槽来改变切屑流出的速度和方向,以达到断屑的目的。工具研究所介绍的断屑槽形状和尺寸如图9-137所示。试验表明,断屑槽的尺寸公差必须限制在很窄的范围内,特别是断屑槽的深度对断屑效果影响很大。
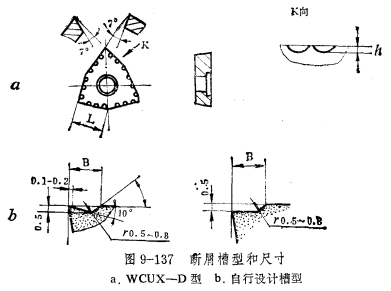
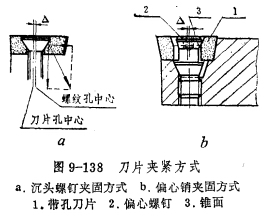
⑦冷却方法:用可转位浅孔钻头钻孔必须强制浇注冷却液,它起着冷却润滑和排屑的双重作用。冷却液的流路如图9-139所示。它又分为下述两种流路:
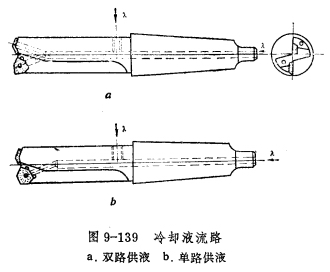
(b)冷却液从钻头体中段或尾端的孔流入钻头体,从位于钻头切削刃前面的两个出水孔流出浇到切削区域后返回,在返回途中带着切屑沿排屑沟排出孔外。
直径小的钻头可采用两种流路相结合的方式,以加强排屑的作用。
(3)钻头各部分尺寸的确定
①钻心直径:硬质合金浅孔钻头的钻心直径do=(0.25~0.5)D,D为钻头直径。由于刀杆内部钻有内冷却孔,故钻心直径不能太小。设计时一般取do=0.35D。
②钻头直径公差:刀片位置的偏差可使孔径扩大或缩小。此外,还有进给量的影响,进给量越大,孔的直径扩张量也越大。但切削速度增加时,则孔的直径可稍有缩小。孔的圆度和圆柱度,主要取决于工件一刀具一机床系统的刚性,一般不超过0.02mm,可取与硬质合金麻花钻头公差相同的值。如在车床上钻孔,当孔径在50mm以下时,圆度误差在0.02~0.06mm范围内。
③两切削刃的搭接量:以分屑方式配置的两切削刃的衔接处应有一定的搭接量,其数值为2~5mm。这样可使一种规格的刀片能用于多种规格的钻头上,减少了刀片规格。
硬质合金可转位浅孔钻的出现,使孔加工的切削效率空前提高。所以,使其得到了广泛的应用。
- 上一篇:硬质合金可转位钻头
- 下一篇:镶齿冠的硬质合金麻花钻