技术支持
地 址:湖南省安化县高明乡工业园
手 机:137-8611-1081
电 话:0737-7411519
传 真:0737-7411519
联系人:薛经理
Q Q:28288453

钨钴硬质合金刀具的性能
时间:2015-07-16 16:42:01来源:本站人气:3667
钨钴硬质合金早在本世纪三十年代初期就被用于机械加工车间,它使机床的生产能力发生了一次革命,其影响如同高速钢出现时那样巨大。经过多年的使用实践,在刀具几何形状、机床结梅、加工方法,以及操作人员的心情态度等方面都已作了合适的改进,从而使硬质合金刀具能够更加有效地应用。如果能够防止过早的断裂,硬质合金刀具就能以很高的切削速度切削多种金属和合金,而且具有很长的刀具寿命。对它的金属切除率要有一定联制,以便使刀具具有合理的刀具寿命。在使用高速钢刀具时,由予连续使用,切削刃的形状就逐渐变化,直到刀具不再能有效地切削。而在使用钨钴合金刀具切削铸铁、钢和高熔点合金时,如果要仔细研究切削刃形状变化的机理和过程,首先应该检查对金属切除率的限制[24][25][26]。
当用高速钢刀具在中等和较高切削速度下切削铸铁和钢时,工件材料会粘结到刀具被磨损的前刀面和后刀面上。所以如同叙述过的工具钢刀具那样,具有同样特征的流变层就是热源。高速钢的第一种磨损机理(在刀具前刀面上因剪切形成月牙洼磨损),在使用硬质合金刀具时不会出现,因为在高温时,硬质合金的抗剪强度很高,不会发生这种情况。
压应力作用下的塑性变形
当切削速度或进给量增加时,由于前刀面上压应力也增大,因而使刀具发生塑性变形,为此,必须限制金属切除率。硬质合金仅能承受有限的变形,在较高的温度下,如存在裂纹,就会导致刀具突然断裂。图6.29表示了前刀面上的这种裂缝,这个表面在切削刃发生塌陷时,受到拉伸应力的作用。由于变形引起的刀具损坏,大都是因为进给量过高和切削具有高硬度的材料。含钴量较低的硬质合金牌号,可以使用较高的切削速度和进给量,因为它们抵抗变形的性能有所增加。细晶粒的硬质合金在室温下的硬度有所提高,但并不意昧着在高温时刀具抵抗变形的能力也有了改善。
在实验室的刀具试验中,可以在较早的阶段发现刀具的变形,其方法是在试验前把后刀面研磨成光学平面,在试验后用光学干涉仪观察这个平面,这样在后刀面上的任何不规则的突起状变形都能被观察到,而且可以用干涉条纹形成的轮廓图进行测量。图6.30表示用硬质合金刀具在以高速和大进给量切削钢件时后刀面上的干涉条纹。可以看到最大变形是在刀尖上,这是在切削钢件和铸铁时的共同特点。刀尖锋利的刀具或刀尖圆弧半径非常小的刀具,变形和损坏都是首先从刀尖处开始,因而对于刀尖圆弧半径小的刀具必须采用较低的速度。在很多切削过程中,刀尖圆弧半径的准确形状是衡量刀具性能的标志。
钨钴硬质合金刀具在高温时具有抵抗变形的能力,因而它可以采履比高速钢刀具更高的金属切除率,这是它的最重要的性能。
扩散磨损
当在高速和大进给量条件下切削钢件时,在钨钴硬质合金刀具的前刀面上会形成一个月牙洼,而在切削刃处有一个未磨损的平面(图6.31)。硬质合金刀具的温度测量方法不同于高速钢刀具,但是它们的温度梯度的型式还是相同的,这是因为具有同样特征的热源—与前刀面接触的薄的金属流变层。其月牙洼的位置也与高速钢刀具相同,较深的月牙洼和高温区有密切关系,而未磨损的平面和刀刃附近的低温区有关。从WC-Co合金刀具的月牙洼磨片图中看不到在刀具材料上有剪切引起的塑性变形。碳化物晶粒均匀地磨损(图6.32),逐渐变小或脱落,在光学显微镜下能看到的颗粒会从刀具表面上脱落。
在WC-Co含金刀具的月牙洼磨损过程中,扩散现象非常明显,刀具中的金属原子和碳原子扩散到粘结在刀具表面上的工件材料中去,并被切屑带走。在这方面的一个极端的例子,是WC-Co硬质合金的硬颗粒嵌进到钢板里,这是在研究界面的磨片图时观察到的。这个例子表明碳化钨WC和钴Co已溶解在钢的表层中,而这个表层在界面上也已经熔化[27]。图6.33就是表示这样的磨片,上面是钢,下面是硬质合金,中间白色的就是熔化层,它是处于局部熔解的区域之中,WC晶粒就被围在中间。WC和钴之间或WC和铁之间的低共熔点大约学1300℃,在界面处的薄层中这个温度已经达到。因为在这种情况下冲击速度已超过1000米/秒,有巨大的能量在极短的时间内转变为热量。
WC-Co合金刀具切削钢件时产生的月牙洼磨损,是由于在1300℃温度下的界面上发生熔化的结果。然而,当切削刀具的切削速度小100倍,像高速钢刀具那样,仍有明显的温度分布,例如图5.3指出的,界面的温度低于1300℃,在这种条件下,月牙洼磨损可能首先发生在900-1100℃的区域内。这个温度低于熔化的温度,但它足以引起在固态相发生扩散,观察到的表面特征也是和由于固态相扩散引起的磨损过程相一致的。
磨损的硬质合金刀具可以用盐酸HCl或别的矿物酸进行处理,清除掉粘着的钢和铁,因此对刀具表面的磨损区可以进行详细研究。当酸在一定程度上溶解了粘结剂钴以后,它们也不能侵蚀碳化物,因而这种硬质合金刀具磨损的检验方法不可能用于高速钢刀具。图6.34和图6.35表示了WC-Co合金刀具在切削钢件以后的月牙洼磨损表面,碳化物晶粒主要是均匀地磨损掉,但有时会出现一种被蚀刻的外貌,如在图6.35中的大晶粒刻痕。这种在刀具表面上留下的刻痕,是平行于一个主要结晶方向。另外在刀具表面上常常可以看到光滑的隆起线,这种线从大的WC。晶粒开始发生,通向切屑流动的方向。如图6.34所示。月牙洼磨损的特点是表面非常光滑,这是因为工件材料快速地从刀具表面上流过,起到了抛光作用。而在这个区域中出现的刻痕,是由于该处的温度相当高,使工件材料的流动速度降低,或是由于界面上存在着滞留层。
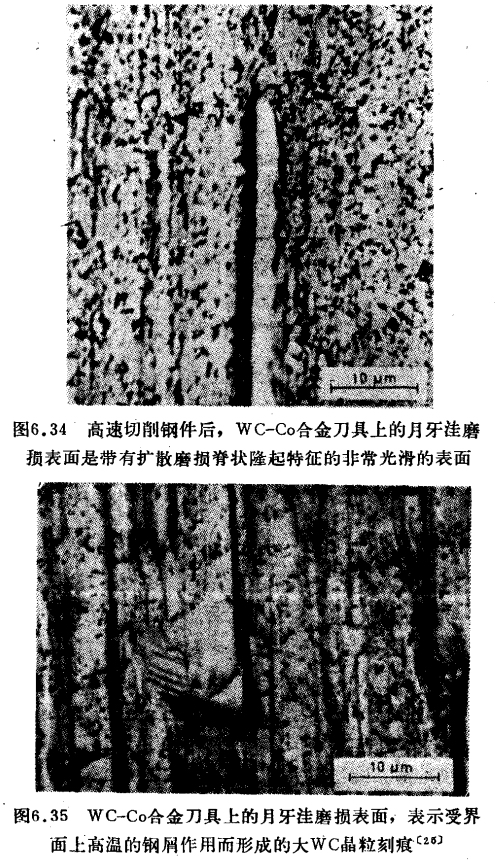
由于扩散引起的月牙洼磨损仅仅在较高的金属切除率的情况下发生。硬质合金刀具上的这种磨损特点以及其他类型的磨损特点,可以用图6.36所示的“加工图表”简易方便地描述[35]。图上的座标为切削速度和进给量,是用对数座标表示的,对角的虚线是表示金属切除率相等的线。对于每一种刀具和工件材料的组合,在使用标准几何形状的刀具时,所产生的主要磨损特点都可以对应地描绘出一种加工图表。图6.36中的两条线是表示刚开始出现月牙洼磨损的切削条件和月牙洼磨损已经非常严重,以至在几分钟内就会引起刀具损坏的切削条件。图6.36是用含有6%的钨钴合金刀具切削中碳钢时的加工图表。由于扩散引起的月牙洼磨损是切削速度和进给量的函数,而且在很广泛的切削条件范围内存在着近似的线性关系。例如为防止产生快速的月牙洼磨损,在进给量为0.25毫米/转时,切削速度的极限值应为90米/分,而在进给量为0.75毫米/转时,临界速度应减小到35米/分。这些图表和最大的切削速度数字,表明了在使用WC-Co硬质合金刀具切削钢件时,在限制金属切除率中因扩散引起的月牙洼磨损的重要性。WC-Co硬质合金刀具的最大金属切除率比起高速钢刀具来并不很高,所以它不经常用来切削钢件。它们主要被推荐甩于切削铸铁和有色金属。但它们在较低的切削速度下切削钢件时,有刀具寿命较长的优点。
由于扩散磨损对于硬质合金刀具是这样重要,就有必要更详细地考虑这种磨损的机理[6][25]。通过界面的扩散率主要取决于温度,但还有很多其他的因素也有影响。倒如含有的原子相对尺寸,它们的化学作用以及材料彼此之问的可溶性。既然会产生扩散磨损,一定会具有某些可溶性:倒如已经证明,在1250℃时,有7%盼WC溶解在铁中。因此扩散磨损率取决于材料的“兼容性”(compatibility)。使用不同的刀具和工件材料产生的扩散磨损率有很大的不同。刀具的机械性能使刀具有足够的强度和硬度,能够经受所加的应力,但对于扩散磨损,则刀具的化学性能比机械性能有更大的影响。就是因为这个理由,细晶粒硬质合金虽然硬度比较高,但并不表示它们抵抗扩散磨损的能力有所提高。事实上,粗晶粒合金比同样成分的细晶粒合金更耐磨一些,但是这种差别是比较小的。
扩散磨损率还取决于原子从刀具上扩散到工件材料中去的速度。现在经常考虑的问题是“从刀具材料中扩散出来的原子是最重要的吗?”在高速钢刀具的情况下,铁原子从刀具基体上扩散进入到工件中,只剩下孤立的碳化物颗粒,它们逐渐受到损害,最后整个脱落。而在硬质含金刀具的情况下,碳化物的粘结剂钴原子和工件材料的铁原子以最快的速度互相扩散,然而碳化物颗粒不会受到损坏和脱落,这是因为有下面两个原因,首先,因为碳化物颗粒不是孤立的,它们构成了硬质合金的绝大部分体积,它们彼此支承形成一个刚性的骨架,其次,因为刀具虽然有钴原子扩散出去,但有铁原子被吸收进来,而铁原子如同钻原子一样,能有效地粘结碳化物。
碳原子很小,能在铁原子之间快速地运动,但是在刀具中,碳原子和钨强有力地结合在一起,不能自由运动而离去。这样碳原子和钨必须结合在一起,扩散到工件材料中去,扩散磨损率就受到控制。这不仅取决于温度,而且也和非常接近刀具表面的工件材料的流动速度有关系,也就是和工件材料快速流过0.001-1微米距离的速度有关系;正如水的蒸发率在停滞的空气中是很慢的那样,如果接近刀具表面的工件材料是静止的,则刀具的扩散磨损也是很慢的。而在刀具的后刀面,接近刀具表面的工件材料的流动速度是非常高的(图5.1a),甚至在前刀面实际上还未发生磨损的情况下,后刀面已经有很高的磨损率,其主要原因就是后刀面的扩散磨损引起的。在图3.5中,可以看到后刀面上的碳化物晶粒是被均匀地磨损掉的。在发生粘结的条件下,碳化物晶粒均匀地磨损掉,被认为是在扩散磨损过程中的较好的现象。
当在较高的切削速度下切削时,后刀面磨损主要是扩散磨损引起的,切削速度提高,磨损率也迅速增加。图6.37表示了用硬质合金刀具以较高的切削速度切削钢件时所获得的一组典型的刀具磨损曲线。钨钴合金中的钴含量对扩散磨损率有影响,当钴含量增加时j后面磨损率也增大。但是,用于切削的通用牌号硬质合金,当刀具没有开始变形时,其磨损率的差别不是很大的。
摩擦磨损
用高速钢刀具以较低的速度切削时,因为温度不高,不会发生扩散磨损和严重的变形,这时,摩擦就成为引起磨损的主要支配因素。当工件材料少量的以层状切屑、大量的以断续切屑流经切削刃的条件下,最明显的迹象就是形成积屑瘤。图6.36是很多种钢的典型加工图表,图中表示积屑瘤存在于比较低的金属切除率情况下,它主要取决于切削速度和进给量。图中积屑瘤线的下面部分,其磨损主要由摩擦所支配。积屑瘤由工件材料组成,切削时,它连续地变化;成碎片剪离(图3.15)。如果积屑瘤仅外层被剪离,而接近刀具那部分积屑瘤仍然粘附在刀具上没有变化,则刀具还可以继续切削很长的时间而不会被磨损。例如在有些情况下,切削铸铁时,即使在较高的切削速度和进给量下,积屑瘤还粘附在WC-Co合金刀具上,如图6.38中的加工图表所示的那样。在切削灰铸铁时,积屑瘤极少碎离,所以刀具寿命非常长。就因为这个理由,WC-Co合金刀具通常用来切削铸铁时所推荐的切削速度,就是在能形成积屑瘤的范围内。图3.8和图3.9的磨片图表示了刀具上碳化物晶粒的碎片或整个晶粒脱落后遗留下来的这种磨损表面,这种因为摩擦引起的磨损率是比较低的。
然而用WC-Co合金刀具切削钢时,在能形成积屑瘤的条件下,刀具切削刃可能很侠地因摩擦而损坏。在使用高速钢刀具时,只有显微尺寸的刀具材料碎片可以从刀刃上撕离 下来,这是一种较慢的磨损机理,但对于硬质合金刀具来说,它可能引起很快的磨损。如果积屑瘤稳定地粘结在刀具上,有时突然作为一个整体脱落下来,刀刃上可能会被撕下较大的碎片,如图6.39所示,就会经常发生中断切削的现象当机床缺乏刚度,或者工件是细长的,就容易发生颤振和振动,则流经刀具的金属流可能非常不规则;就会从刀具上撕下较小的碎片。图6.40表示,用WC-Co合金刀具在较低的切削速度和进给量条件下切削钢件时,WC晶粒被破坏并被切屑流带走。
碎片的分离是因不规则的金属流所加在刀具上的局部拉应力引起的。高速钢刀具因为有较大的延展性和韧性,所以能经受较大的拉应力,因而具有较大的抵抗摩擦磨损的能力。这就是为什么很多在低速下进行的加工工序现在还在使用、并且将来还要继续使用高速钢刀具的主要原因之一。由摩擦产生的磨损表面,与因扩散磨损产生的几乎像经过抛光的磨损表面相比,是非常粗糙的。然而,在这两种磨损形式之间并没有明显的分界线,它们是同时发生的。所以在磨损表面上,当粘结着的金属被溶解掉以后,常常可以发现有些晶粒被均匀地磨损妒而另外一些晶粒已被撕离。如图6.41。
由摩擦引起的磨损率,不是直接与刀具的硬度有关,对于WC-Co硬质合金刀具来说,最重要的因素是晶粒尺寸。细晶粒合金比粗晶粒合金具有更好的耐磨性。图6.42表示含有6%钴的一组刀具的磨损率,这些数据是在实验室的试验中,在摩擦磨损的条件下切削铸铁时获得的。硬度数字就代表了碳化物的晶粒尺寸,最高的硬度表示小于1微米的超细晶粒尺寸。通过比较可知,含钴量对摩擦磨损率的影响较小。图6.43表示含钴量为5.5-20%的各种硬质合金刀具的磨损率,其差别很小,因为这些刀具具有相同的晶粒尺寸,但硬度差别却较大。在这种条件下,要使这些合金的性能保持一致,就应在制造细晶粒合金时严格控制晶粒尺寸。
由于在切削刃周围的金属流在切削速度增加时趋向于变成层状切屑,所以摩擦磨损率在切削速度下降时可能会增加。图6.44表示在摩擦磨损条件F切削铸铁时后刀面磨损率的一组曲线,可以和表示扩散磨损的图6.37进行比较。在摩擦磨损占主导地位的博况下,为r改善刀具寿命,应把注意力放在减少振动、增加刚度以及给刀具设计足够大的后角等方面。
磨料磨损
由于碳化钨具有很高的硬度,所以磨料磨损对于硬质含金刀具来说不是一种重要的磨损过程。这与高速钢刀具是不一样的。只有在切削时存在大量的研磨材料时,例如铸件表面上的砂子,才会使刀具具有少量的磨损痕迹。在粘结条件下,工件材料中的硬碳化物或氧化铝的孤立的微小颗粒,能有效地腐蚀碳化物晶粒之间的钴,不过这种情况是极少有的。切削冷硬铸铁轧辊肘,因工件上存在很多渗碳体和其他的碳化物。因此会使刀具产生磨料磨损。但是大多数碳化物,甚至在合金铸铁中,它们的硬度也是低于碳化钨的。关于这种情况下的磨损机理的详细研究还没有报道过。为了防止磨料磨损,最重要的方法是降低硬质合金中的钻含量。另外细化晶粒尺寸也是有用的方法。
断裂
刀具寿命的不稳定,常常是由予刀具在达到磨损限度前就断裂所造成的。在选择刀具材料牌号时,韧性是一个重要的性熊指标。为了改善这个性能,可以增加硬质合金的含钴量或增大晶粒尺寸,这在前面已讨论过。另外还必须更多地注意判断引起断裂的原因,以便能决定采取正确的防护措施。
刀具在连续切削与工件保持接触时,很少发生刀刃部分断裂的现象。大量的刀具断裂都是发生在切削刚开始的时候,特别是在刀刃碰到工件台肩,因而使整个刀刃都突然切入工件的时候。间断切削和铣削加工时也特别容易发生断裂,这可能是由于机械疲劳而断裂。还有切屑缠绕在刀具上或卷在刀刃上,也常常会使切削中未切入工件的刀刃部分因碰撞而引起断裂。在车削大的锻件或铸件时,如果协削深度不均匀,也很容易引起刀刃断裂。
断裂还可能是由于刀具的变形而引起的。随着变形的增加就会产生裂缝。机械断裂不过是刀具损坏的最终阶段。这种情况更说明正确判断断裂原因的重要性。为了防止在这种情况下的刀具损坏,可使用更高硬度的硬质合金,以防止初始的塑性变形。但是高硬度的硬质合金缺乏韧性。所以防止断裂这个问题,光用改变硬质合金牌号的方法是很难解决的,通常还应该包括改变刀具几何形状和切削条件来实现。
热疲劳
在非常频繁的间断切削中,例如铣削时,在刀具上常常可以观察到很多短的、向垂直于切削刃的方向延伸的裂纹,如图6.45所示。刀具在切削时因受切削热作用而产生膨胀,在切削中断时因把热量传给刀体而受到冷却,因而产生收缩。裂纹就是由于刀具表面层的这种交替的热胀冷缩现象引起的。裂纹通常都是在前刀面上离刀刃有一定距离的最热位置上开始产生,然后扩展,横过刀刃,一直发展到后刀面上。硬质合金铣刀在使用过以后,在刀齿上常常可以发现很多这样的裂纹。但是,在大多数情况下对它们的寿命没有多大的影响。如果裂纹非常多,可能会连接起来,使刀刃形成小碎片而崩离。它们也可能引起应力集中,在其他因素作用下,使刀具发生断裂。所以,很多硬质合金制造厂都选用具有对热疲劳不敏感的成分和结构的硬质合金牌号,来作为制造铣刀的刀具材料。
在滑动条件下的磨损
在刀具和工件的界面上发生滑动,常常会产生加速磨损的现象这和高速钢刀具的情况是一样的。图6.46表示了一个突出的例子,它是用WC-Co硬质合金刀具在空气中切削钢件的情况下,由于切屑的边缘滑过前力面而形成了深槽。这里的磨损机理可能包括同空气的反应,这将在有关切削液的第八章中进一步讨论。在同样的切削条件下,滑动比粘结 可能引起更快的磨损,这种现象是很引人注意的。所以,在很多切削工序中,光是消除粘结现象并不十分符合实际情况的。在滑动区内的磨损率:主要是受化学作用的控制,刀具材料的成分比它的硬度或其他的机械性能有更大的影响。
以上介绍了硬质合金刀具磨损或变形的主要机理和过程,其中很多磨损机理是和高速钢刀具相同的,作为总结,可以参考图6.19。第一种磨损机理是不能正常地观察到的。第二种和第三种磨损机理是由于变形和扩散引起的,它主要取决予温度,在高的切削速度下起作用。第四种磨损机理,摩擦磨损,它不取决于温度,在较低的切削速度范围内,对刀具有很大的破坏作用,而在这种情况下,高速钢刀具常常具有相同的或者更好的性能。第五种磨损机理,磨料磨损,可能是最少引起磨损的,比起高速钢刀具来是很不重要的磨损形式。第六种磨损机理,滑动磨损过程,和高速钢一样,都是很重要的一种磨损形式,刀具上发生磨损的位置也是相同的。另外,硬质合金刀具切削刃很容易因断裂而损坏,热疲劳引起的裂纹也能缩短刀具的寿命。在实际加工过程中,正确识别决定刀具寿命的因索,对于选择最佳刀具材料、刀具形状或切削条件的实际操作人员,和对于从事研制新刀具材料、新型刀具或润滑遮的研究人员,都是非常重要的。
当用高速钢刀具在中等和较高切削速度下切削铸铁和钢时,工件材料会粘结到刀具被磨损的前刀面和后刀面上。所以如同叙述过的工具钢刀具那样,具有同样特征的流变层就是热源。高速钢的第一种磨损机理(在刀具前刀面上因剪切形成月牙洼磨损),在使用硬质合金刀具时不会出现,因为在高温时,硬质合金的抗剪强度很高,不会发生这种情况。
压应力作用下的塑性变形
当切削速度或进给量增加时,由于前刀面上压应力也增大,因而使刀具发生塑性变形,为此,必须限制金属切除率。硬质合金仅能承受有限的变形,在较高的温度下,如存在裂纹,就会导致刀具突然断裂。图6.29表示了前刀面上的这种裂缝,这个表面在切削刃发生塌陷时,受到拉伸应力的作用。由于变形引起的刀具损坏,大都是因为进给量过高和切削具有高硬度的材料。含钴量较低的硬质合金牌号,可以使用较高的切削速度和进给量,因为它们抵抗变形的性能有所增加。细晶粒的硬质合金在室温下的硬度有所提高,但并不意昧着在高温时刀具抵抗变形的能力也有了改善。
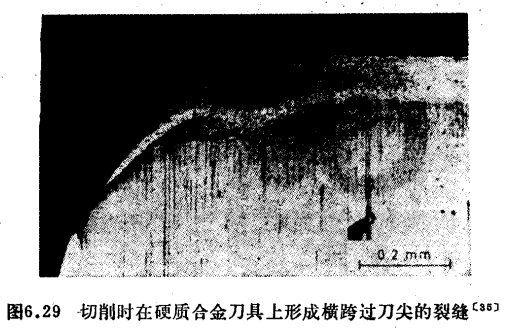
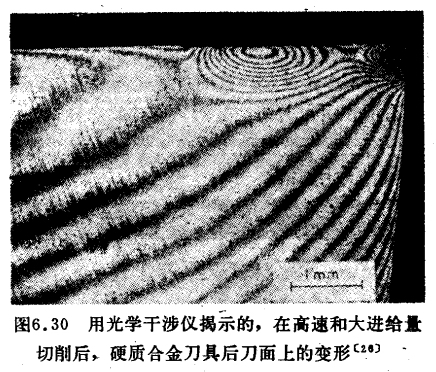
扩散磨损
当在高速和大进给量条件下切削钢件时,在钨钴硬质合金刀具的前刀面上会形成一个月牙洼,而在切削刃处有一个未磨损的平面(图6.31)。硬质合金刀具的温度测量方法不同于高速钢刀具,但是它们的温度梯度的型式还是相同的,这是因为具有同样特征的热源—与前刀面接触的薄的金属流变层。其月牙洼的位置也与高速钢刀具相同,较深的月牙洼和高温区有密切关系,而未磨损的平面和刀刃附近的低温区有关。从WC-Co合金刀具的月牙洼磨片图中看不到在刀具材料上有剪切引起的塑性变形。碳化物晶粒均匀地磨损(图6.32),逐渐变小或脱落,在光学显微镜下能看到的颗粒会从刀具表面上脱落。
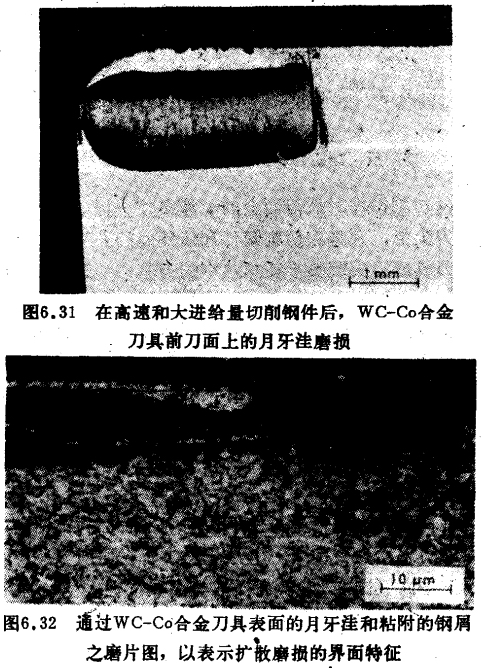
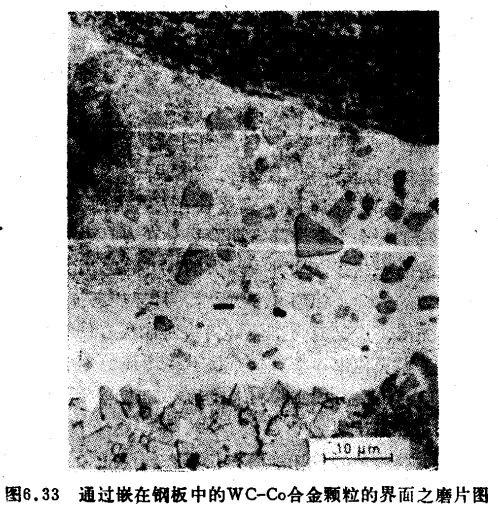
磨损的硬质合金刀具可以用盐酸HCl或别的矿物酸进行处理,清除掉粘着的钢和铁,因此对刀具表面的磨损区可以进行详细研究。当酸在一定程度上溶解了粘结剂钴以后,它们也不能侵蚀碳化物,因而这种硬质合金刀具磨损的检验方法不可能用于高速钢刀具。图6.34和图6.35表示了WC-Co合金刀具在切削钢件以后的月牙洼磨损表面,碳化物晶粒主要是均匀地磨损掉,但有时会出现一种被蚀刻的外貌,如在图6.35中的大晶粒刻痕。这种在刀具表面上留下的刻痕,是平行于一个主要结晶方向。另外在刀具表面上常常可以看到光滑的隆起线,这种线从大的WC。晶粒开始发生,通向切屑流动的方向。如图6.34所示。月牙洼磨损的特点是表面非常光滑,这是因为工件材料快速地从刀具表面上流过,起到了抛光作用。而在这个区域中出现的刻痕,是由于该处的温度相当高,使工件材料的流动速度降低,或是由于界面上存在着滞留层。
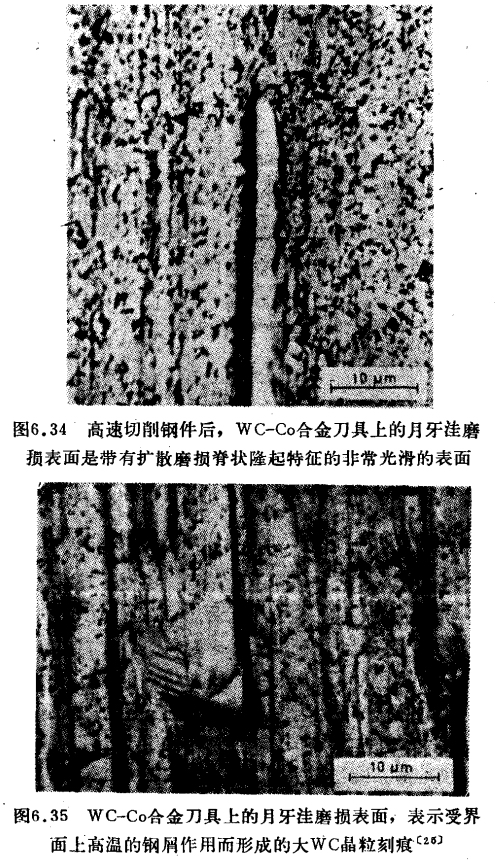
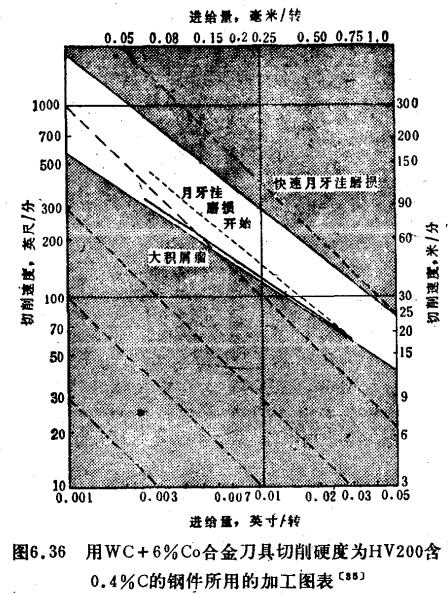
扩散磨损率还取决于原子从刀具上扩散到工件材料中去的速度。现在经常考虑的问题是“从刀具材料中扩散出来的原子是最重要的吗?”在高速钢刀具的情况下,铁原子从刀具基体上扩散进入到工件中,只剩下孤立的碳化物颗粒,它们逐渐受到损害,最后整个脱落。而在硬质含金刀具的情况下,碳化物的粘结剂钴原子和工件材料的铁原子以最快的速度互相扩散,然而碳化物颗粒不会受到损坏和脱落,这是因为有下面两个原因,首先,因为碳化物颗粒不是孤立的,它们构成了硬质合金的绝大部分体积,它们彼此支承形成一个刚性的骨架,其次,因为刀具虽然有钴原子扩散出去,但有铁原子被吸收进来,而铁原子如同钻原子一样,能有效地粘结碳化物。
碳原子很小,能在铁原子之间快速地运动,但是在刀具中,碳原子和钨强有力地结合在一起,不能自由运动而离去。这样碳原子和钨必须结合在一起,扩散到工件材料中去,扩散磨损率就受到控制。这不仅取决于温度,而且也和非常接近刀具表面的工件材料的流动速度有关系,也就是和工件材料快速流过0.001-1微米距离的速度有关系;正如水的蒸发率在停滞的空气中是很慢的那样,如果接近刀具表面的工件材料是静止的,则刀具的扩散磨损也是很慢的。而在刀具的后刀面,接近刀具表面的工件材料的流动速度是非常高的(图5.1a),甚至在前刀面实际上还未发生磨损的情况下,后刀面已经有很高的磨损率,其主要原因就是后刀面的扩散磨损引起的。在图3.5中,可以看到后刀面上的碳化物晶粒是被均匀地磨损掉的。在发生粘结的条件下,碳化物晶粒均匀地磨损掉,被认为是在扩散磨损过程中的较好的现象。
当在较高的切削速度下切削时,后刀面磨损主要是扩散磨损引起的,切削速度提高,磨损率也迅速增加。图6.37表示了用硬质合金刀具以较高的切削速度切削钢件时所获得的一组典型的刀具磨损曲线。钨钴合金中的钴含量对扩散磨损率有影响,当钴含量增加时j后面磨损率也增大。但是,用于切削的通用牌号硬质合金,当刀具没有开始变形时,其磨损率的差别不是很大的。
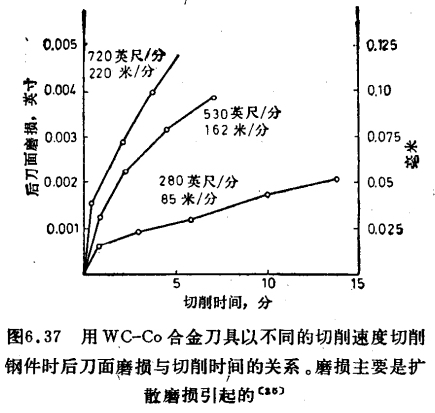
用高速钢刀具以较低的速度切削时,因为温度不高,不会发生扩散磨损和严重的变形,这时,摩擦就成为引起磨损的主要支配因素。当工件材料少量的以层状切屑、大量的以断续切屑流经切削刃的条件下,最明显的迹象就是形成积屑瘤。图6.36是很多种钢的典型加工图表,图中表示积屑瘤存在于比较低的金属切除率情况下,它主要取决于切削速度和进给量。图中积屑瘤线的下面部分,其磨损主要由摩擦所支配。积屑瘤由工件材料组成,切削时,它连续地变化;成碎片剪离(图3.15)。如果积屑瘤仅外层被剪离,而接近刀具那部分积屑瘤仍然粘附在刀具上没有变化,则刀具还可以继续切削很长的时间而不会被磨损。例如在有些情况下,切削铸铁时,即使在较高的切削速度和进给量下,积屑瘤还粘附在WC-Co合金刀具上,如图6.38中的加工图表所示的那样。在切削灰铸铁时,积屑瘤极少碎离,所以刀具寿命非常长。就因为这个理由,WC-Co合金刀具通常用来切削铸铁时所推荐的切削速度,就是在能形成积屑瘤的范围内。图3.8和图3.9的磨片图表示了刀具上碳化物晶粒的碎片或整个晶粒脱落后遗留下来的这种磨损表面,这种因为摩擦引起的磨损率是比较低的。
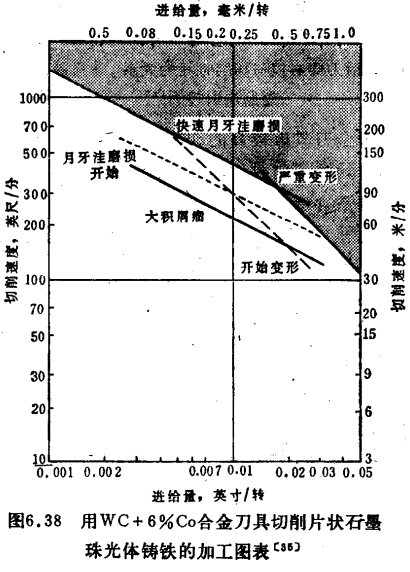
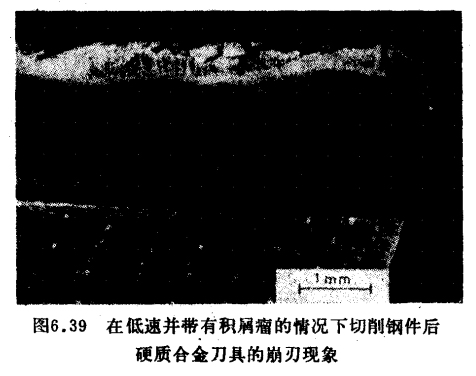
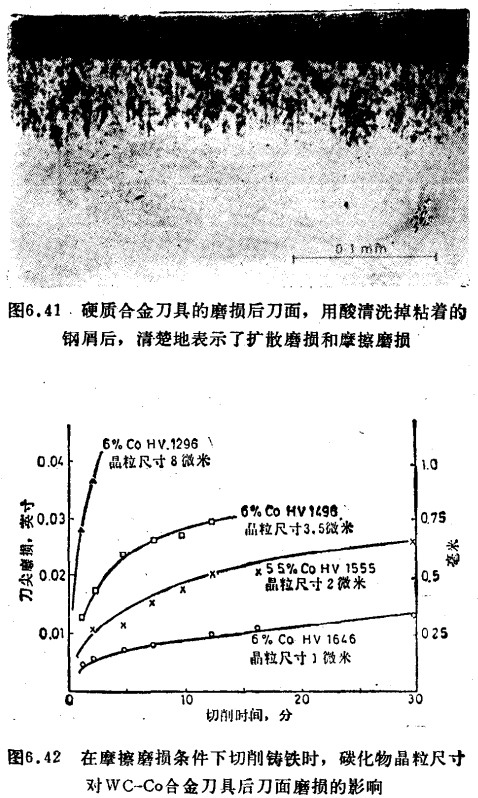
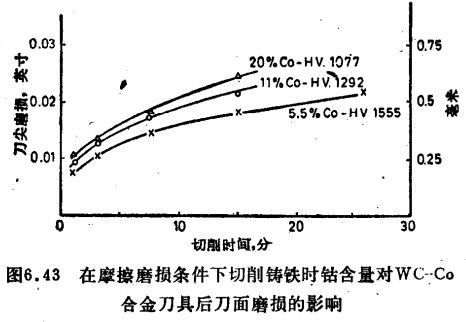
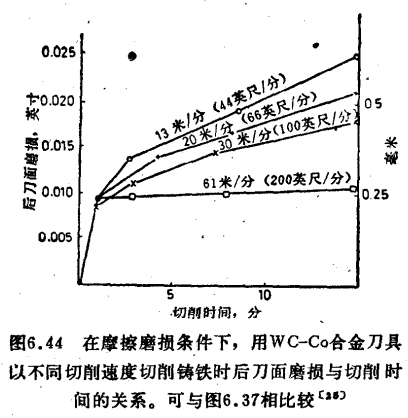
由于碳化钨具有很高的硬度,所以磨料磨损对于硬质含金刀具来说不是一种重要的磨损过程。这与高速钢刀具是不一样的。只有在切削时存在大量的研磨材料时,例如铸件表面上的砂子,才会使刀具具有少量的磨损痕迹。在粘结条件下,工件材料中的硬碳化物或氧化铝的孤立的微小颗粒,能有效地腐蚀碳化物晶粒之间的钴,不过这种情况是极少有的。切削冷硬铸铁轧辊肘,因工件上存在很多渗碳体和其他的碳化物。因此会使刀具产生磨料磨损。但是大多数碳化物,甚至在合金铸铁中,它们的硬度也是低于碳化钨的。关于这种情况下的磨损机理的详细研究还没有报道过。为了防止磨料磨损,最重要的方法是降低硬质合金中的钻含量。另外细化晶粒尺寸也是有用的方法。
断裂
刀具寿命的不稳定,常常是由予刀具在达到磨损限度前就断裂所造成的。在选择刀具材料牌号时,韧性是一个重要的性熊指标。为了改善这个性能,可以增加硬质合金的含钴量或增大晶粒尺寸,这在前面已讨论过。另外还必须更多地注意判断引起断裂的原因,以便能决定采取正确的防护措施。
刀具在连续切削与工件保持接触时,很少发生刀刃部分断裂的现象。大量的刀具断裂都是发生在切削刚开始的时候,特别是在刀刃碰到工件台肩,因而使整个刀刃都突然切入工件的时候。间断切削和铣削加工时也特别容易发生断裂,这可能是由于机械疲劳而断裂。还有切屑缠绕在刀具上或卷在刀刃上,也常常会使切削中未切入工件的刀刃部分因碰撞而引起断裂。在车削大的锻件或铸件时,如果协削深度不均匀,也很容易引起刀刃断裂。
断裂还可能是由于刀具的变形而引起的。随着变形的增加就会产生裂缝。机械断裂不过是刀具损坏的最终阶段。这种情况更说明正确判断断裂原因的重要性。为了防止在这种情况下的刀具损坏,可使用更高硬度的硬质合金,以防止初始的塑性变形。但是高硬度的硬质合金缺乏韧性。所以防止断裂这个问题,光用改变硬质合金牌号的方法是很难解决的,通常还应该包括改变刀具几何形状和切削条件来实现。
热疲劳
在非常频繁的间断切削中,例如铣削时,在刀具上常常可以观察到很多短的、向垂直于切削刃的方向延伸的裂纹,如图6.45所示。刀具在切削时因受切削热作用而产生膨胀,在切削中断时因把热量传给刀体而受到冷却,因而产生收缩。裂纹就是由于刀具表面层的这种交替的热胀冷缩现象引起的。裂纹通常都是在前刀面上离刀刃有一定距离的最热位置上开始产生,然后扩展,横过刀刃,一直发展到后刀面上。硬质合金铣刀在使用过以后,在刀齿上常常可以发现很多这样的裂纹。但是,在大多数情况下对它们的寿命没有多大的影响。如果裂纹非常多,可能会连接起来,使刀刃形成小碎片而崩离。它们也可能引起应力集中,在其他因素作用下,使刀具发生断裂。所以,很多硬质合金制造厂都选用具有对热疲劳不敏感的成分和结构的硬质合金牌号,来作为制造铣刀的刀具材料。
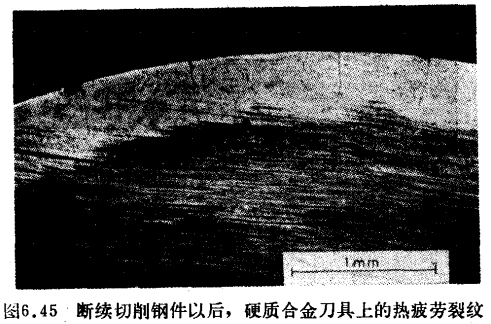
在刀具和工件的界面上发生滑动,常常会产生加速磨损的现象这和高速钢刀具的情况是一样的。图6.46表示了一个突出的例子,它是用WC-Co硬质合金刀具在空气中切削钢件的情况下,由于切屑的边缘滑过前力面而形成了深槽。这里的磨损机理可能包括同空气的反应,这将在有关切削液的第八章中进一步讨论。在同样的切削条件下,滑动比粘结 可能引起更快的磨损,这种现象是很引人注意的。所以,在很多切削工序中,光是消除粘结现象并不十分符合实际情况的。在滑动区内的磨损率:主要是受化学作用的控制,刀具材料的成分比它的硬度或其他的机械性能有更大的影响。
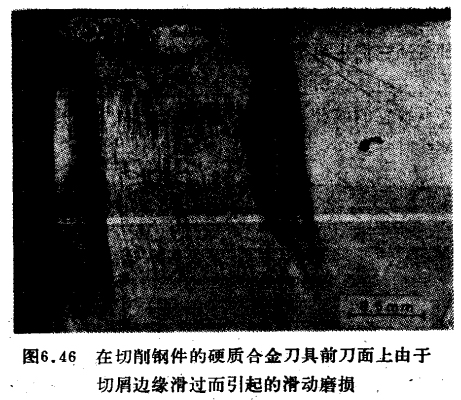
- 上一篇:硬质合金刀具的电解磨削
- 下一篇:硬质合金刀具的安装和固定